In the legal cannabis industry, getting a processed cannabis product can be just as mysterious as buying meat at the grocery store—conveniently packaged and unrecognizable from its original form. And while I appreciate a shroud of mystery around how pigs become sausage, when it comes to cannabis products, I’d actually really like to know how that sausage was made.
This wave of curiosity came to crest with my new favorite cannabis product: a little capsule called RA’, named after the Egyptian sun god. I found myself wondering about the journey the plant material inside had taken: Where did its voyage begin? Did the person who grew it love their job? How did it go from trimmed plant all the way to handy capsule?
I traced my little cannabis pills back to their source and got to talk with some amazing humans on my journey. I found fascinating insights, industry scoops, and people who dedicate their lives to the plant we love.
While you might not want to think about how your sausage was made during breakfast, this is a backstory you’ll love to have in mind when enjoying cannabis products. It is a very human industry, my friends; let’s do our damndest to ensure that it stays that way.
Starting from seed

(Courtesy Sweet Sisters Farm)
Our plant’s journey starts at Sweet Sisters outdoor farm in Mendocino, Northern California, which is part of the Emerald Triangle, an area globally celebrated for its cannabis. Referring to themselves as a “family unit,” they don’t at all claim to be breeders. “The beauty of being a legacy farmer … is that we have had seedstock in our own possession for years, that we know can work well in our own microclimate,” said the family unit.
They’ve been farming the same land since 1981, when the two farmers who started the family unit met at a nursery buying cannabis growing supplies. Since then, they’ve had plenty of time to learn their favorite cultivars, some that go back to the ‘80s—back when they used to have true indicas and sativas, before all the hybridization. They know the growth cycles of various strains, as well as important details like which seeds will be resistant to mold and powdery mildew, and which ones will grow into buds that they enjoy and prefer.
The planting process starts in mid-March by cracking the seeds, which will sex in 6-8 weeks. Then they enjoy watching all of the individual characteristics come out of each plant within the cultivar: “It’s an honor and a pleasure to watch her grow,” said the family unit.
Sometime in September or October, it’s harvest time. After cutting the plants, it’s time to cure; watching the humidity and heat, it’s done in about two weeks, depending on each individual plant. They leave it on the branch so it finishes its final cure and holds better until it can get to the trimmer’s bench. Then they do some paperwork and it’s out of their hands.
On the trimmer’s bench
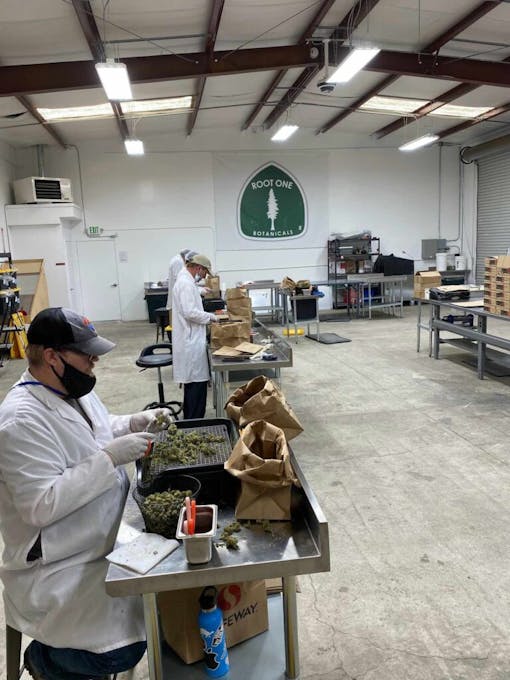
(Courtesy of Root One Botanicals)
From Sweet Sisters farm, our plant heads to Root One Botanicals. They do many things at Root One, but our plant is here to get trimmed. The beautiful buds will be separated from trim, which RA’ does not use in their products. But before it’s time to work with the plant, there’s paperwork to do.
Like many other legal states, California uses a program called Metrc to track each plant from seed to sale. Root One CEO Jon McColley describes the process as “arduous and boring” but also recognizes its importance.
Once harvests come in, plant material gets divided between A, B, and trim, depending on the bud’s size, and waste (stems, etc.) gets tossed out. “It’s segregation, separation, and manicuring; putting those tiered products into their proper place,” said McColley.
McColley reports that the people doing the trimming dig what they do: “It’s amazing what kind of enthusiasm it creates in a workforce … they love the work, being able to work around the plant day after day and just being immersed.”
After our plant has been processed by the Root One crew, it’s tagged and entered into Metrc, then heads out down to Long Beach, California.
The finished capsule
RA’ Flower is our plant’s stop before the dispensary, where it will be made into capsules. According to RA’ Founder and CEO Alan Hoskins, “Once the flower is brought in here, we weigh it, and then I usually try and process it right away just for the sheer fact that cannabis starts the degradation process once it starts growing and being in the sun, and that’s just the natural element. So it’ll come into the building, and then we ‘powderize’ it,” he said, explaining that they use a machine akin to an industrial food mill.
To turn THCa to THC, they blend up the plant and put it through a low heat decarboxylation process. According to Hoskins, the most important part is minimizing the degradation of plants and retaining “important plant constituents, like terpenes, flavonoids, all those wonderful things.”
After the impurities are removed and it’s powderized, “All you’re left with is this really beautiful green powder, which is all flower, decarboxylated,” said Hoskins.
The powder is then tested for potency and terpenes, and Hoskins’ wife, Ashley, takes it away to put into capsules, using a manual machine called an encapsulator, which halves the capsules and puts them back together after they’ve been filled by hand.
Once capsuled, it’s packaging time, and, of course, good ol’ Metrc comes into play here as well. “When [the flower is] brought into the building it has to be entered into Metrc; when I take that flower, and I go to process it, I have to put a new tag on it [for Metrc]; once we decarboxylate it and activate it, it has a new tag; once I put it into packaging, it has another tag,” said Alan, laughing. “So, yeah, it’s very cumbersome. But, you know, it allows the state to really see where every product goes so if there’s a recall on something, they’re able to reach out.”
The Hoskins’ came from the healthcare industry so they’re used to regulations, but not accustomed to the chaos of the cannabis industry. “It’s not an easy business to navigate. It’s over regulated, it’s overtaxed. You know, when there’s 38-40% tax, and people rely on this for medicine, that only helps the black market thrive,” said Alan.
But to them, contributing quality cannabis makes the industry worth it. “It’s about getting a super high-quality product to market, to people who need it. And this is the future of medicine, no doubt,” said Alan.
The other folks involved in the capsule’s journey expressed similar sentiments about the fine art of bringing cannabis to the world. “If there’s just one thing that [readers] should be aware of, it’s that every one of those buds they are consuming has been picked up by loving hands and just been cared for,” said McColley of Root One. “This is the worst get-rich-quick scheme in the history of mankind. The people are doing it because they love the plant and they know that this is something bigger than all of us.”