If you’ve ever been to a cannabis dispensary in Colorado, you’ve probably heard of Ripple—the water-soluble cannabis additive has been popular in the state since its release in November 2016.
Ripple producer Stillwater Brands is now branching out from their flagship product and using the dissolvable to create gummies.
Take a tour with photographer Daniel Brenner at the Stillwater Brands manufacturing facility in Commerce City, Colorado to find out what the buzz is all about.
Ripple: Dissolvable Cannabinoids
Ripple has taken Colorado by storm. The human body absorbs cannabinoids faster if they come dissolved in a liquid, and effects will start to take hold in 15 minutes as opposed to the hour or two for fat-based edibles. This is because water-soluble cannabinoids are mostly absorbed in your mouth and upper intestines, before they hit the liver.
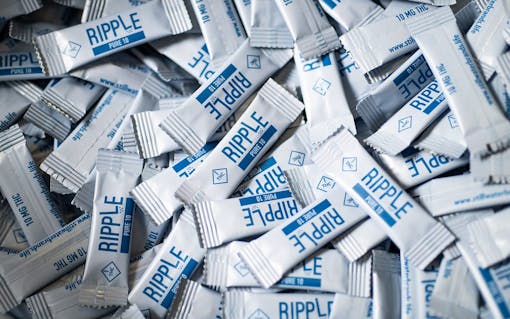
A batch of packaged Ripple Pure 10 at the Stillwater facility in Commerce City, CO. The product contains fast-acting, water-soluble cannabinoids that can be easily introduced to food or liquids with no noticeable impact to flavor, consistency, texture, or appearance. (Daniel Brenner for Leafly)
When THC is metabolized in the liver, as with edibles, most of it leaves the body as waste. Because Stillwater’s Ripple isn’t processed in the liver, its effects only last around two hours. The shorter time frame can be appealing to consumers who aren’t looking to commit a whole day for an edible experience.
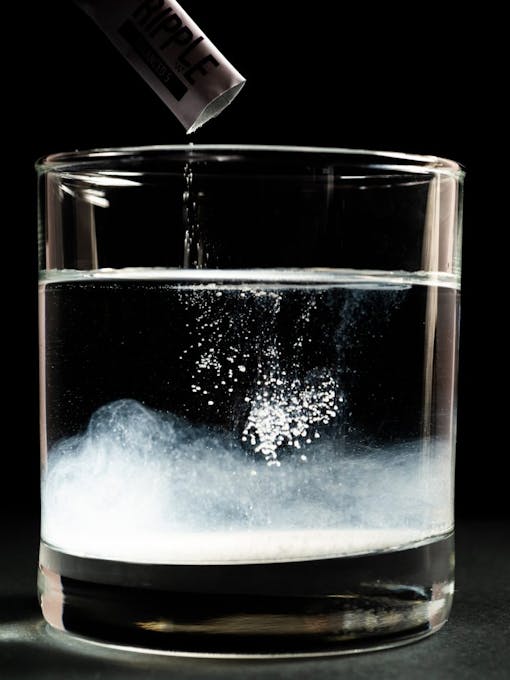
A packet of Stillwater Brands Ripple Balanced 5, containing 5mg THC and 5mg CBD, is poured into water. (Daniel Brenner for Leafly)
Ripple also has a benefit for medical cannabis patients who use a feeding tube. Because it’s water-based, Ripple won’t stick to a tube like other cannabis concentrates.
You can buy it in three versions: pure THC, 1:1 CBD:THC, and 20:1 CBD:THC.
The New Gummy Supplement Line
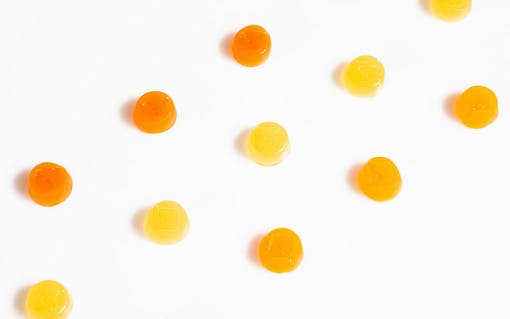
Stillwater Gummy Supplements. From top left: Blood orange, honey lavender, and green tea mango. (Daniel Brenner for Leafly)
Stillwater now produces gummy supplements, using real fruit juice, natural flavors, and organic sugars to create a tasty flavor. To ensure that they’re using the highest quality ingredients, the company constantly evaluates the vendors in their supply chain.
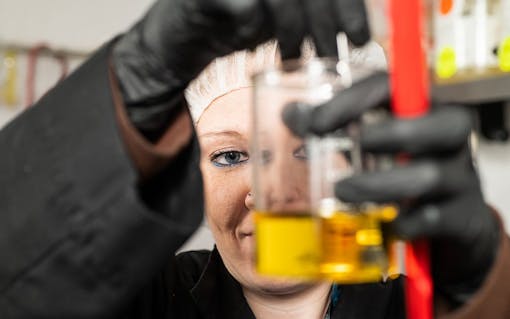
Kitchen lab tech Brittany Sena stirs ingredients for a batch of blood orange gummy supplements. (Daniel Brenner for Leafly)
The process starts with strict control of temperature, moisture, and cook time. Consistency is the key to quality. Even a tiny difference in temperature or moisture can ruin the gummies, and to preserve the integrity of the cannabinoids, Ripple is added at the very end of the cooking cycle. Unlike oil-soluble distillates, which can be difficult to mix in evenly, Ripple disperses throughout the mixture with very little effort.
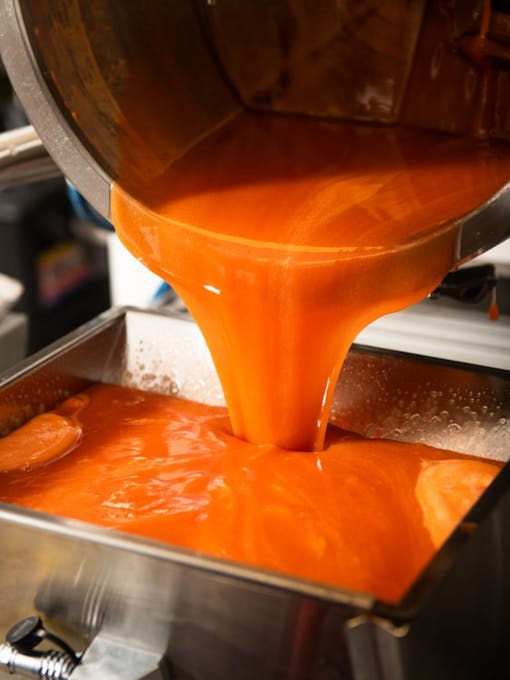
Blood orange gummy supplements are prepared to be poured into a silicone mold. The gummies are made with high quality distillate, real fruit juice, natural flavors, natural colors, and their own Ripple. (Daniel Brenner for Leafly)
Stillwater continues to strive to make their products better. “If you want high-quality products, you’ve got to constantly drive out variance in the process,” says Keith Woelfel, Director of R&D. “Quality is never about just one thing. It’s a combination of your ingredients, your formulation, and your process, which is an enormous factor in the mix. My job is to bring them all together to create the best product in the industry.”
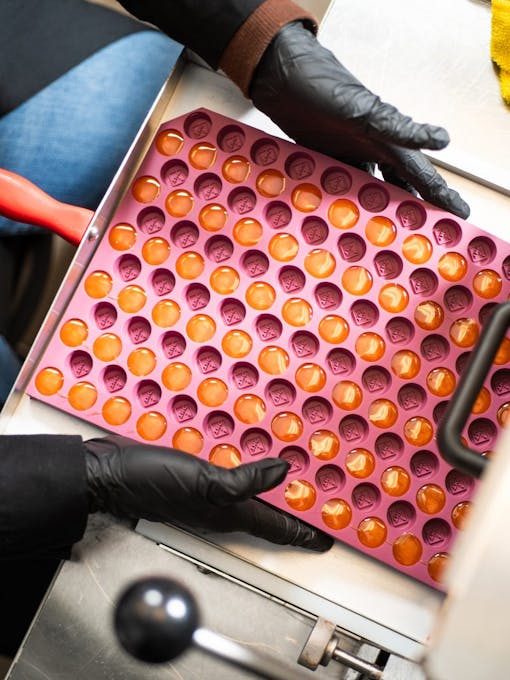
Blood orange gummy supplements are injected into a silicone mold. (Daniel Brenner for Leafly)
Before the gummies are dispensed into molds, the liquid is checked to ensure it has the right percentage of soluble solids. If the result is off by even two percentage points, the gummies will be too hard or sticky to take out. A highly trained employee then pumps a measured amount of gummy liquid into silicone molds by hand. After a 24-hour conditioning period, a three-member team removes each gummy from its mold, at a rate of 18,000 gummies per day.
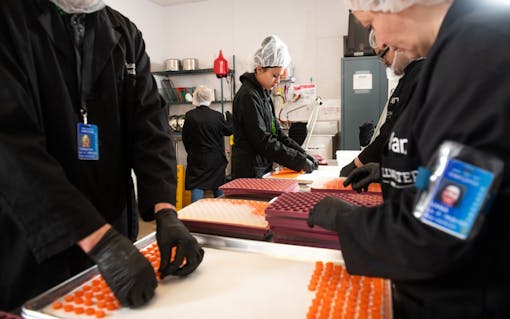
Gummy supplements are separated from a silicone mold and placed on a sheet. (Daniel Brenner for Leafly)
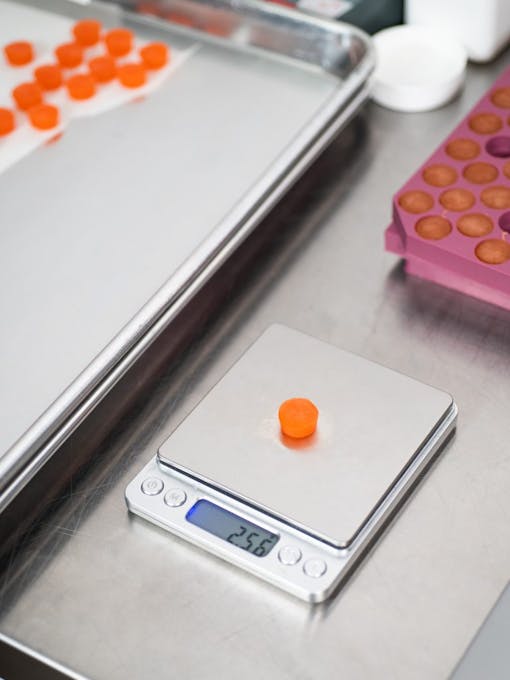
A gummy supplement is weighed. (Daniel Brenner for Leafly)
Weight control is critical to ensure standardized dosing. Although Colorado allows a 15% variance in product weights, Stillwater allows no more than a 5% variance with its gummies. To ensure that their standards are met, an employee weighs a sample of each batch to ensure that weights are within the acceptable range.
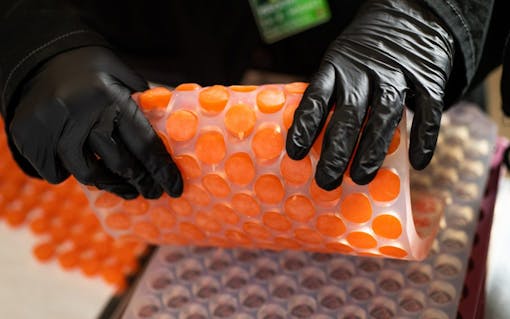
Gummies are separated from a silicone mold and placed on a sheet. (Daniel Brenner for Leafly)
Instead of coating gummies with sugar or citric acid, Stillwater lets their gummies condition for another 24 hours after demolding and then tumbles them with high-quality carnauba wax. This process seals in moisture and keeps the gummies from sticking to each other.
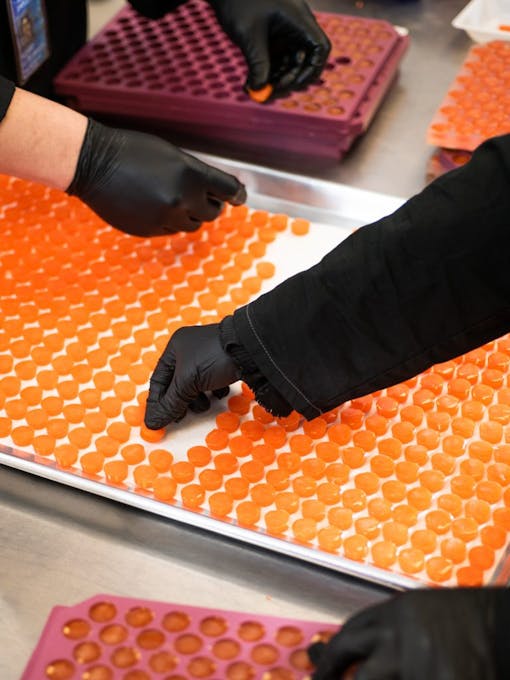
(Daniel Brenner for Leafly)